Introduction
The press brake plays a vital role in the metal processing industry. It is a mechanical equipment specially used to bend metal sheets. By precisely controlling the bending angle and force, press brakes can process sheet metal into various shapes and sizes and are widely used in construction, automotive, aerospace and other manufacturing fields. Its high efficiency and high precision make the press brake one of the indispensable tools for metal processing.
Proper maintenance of a press brakeis of vital importance to ensure its long-term stable operation and avoid common failures. Regular cleaning, lubrication and inspections can significantly extend the service life of your press brake and reduce production delays and repair costs caused by equipment failure. Maintenance work includes not only the hardware part, but also the updating and calibration of the software system to ensure that the press brake is operating at its best.
In the following discussion, we will explore in detail some common press brake failures and their solutions. These failures include, but are not limited to: hydraulic system leaks, mold wear, inaccurate sheet bending, and electrical control system failures. By analyzing the causes and manifestations of these failures, we will provide corresponding solutions to help operators quickly diagnose and repair problems, thereby ensuring efficient operation of the press brakeand improvement of production quality.
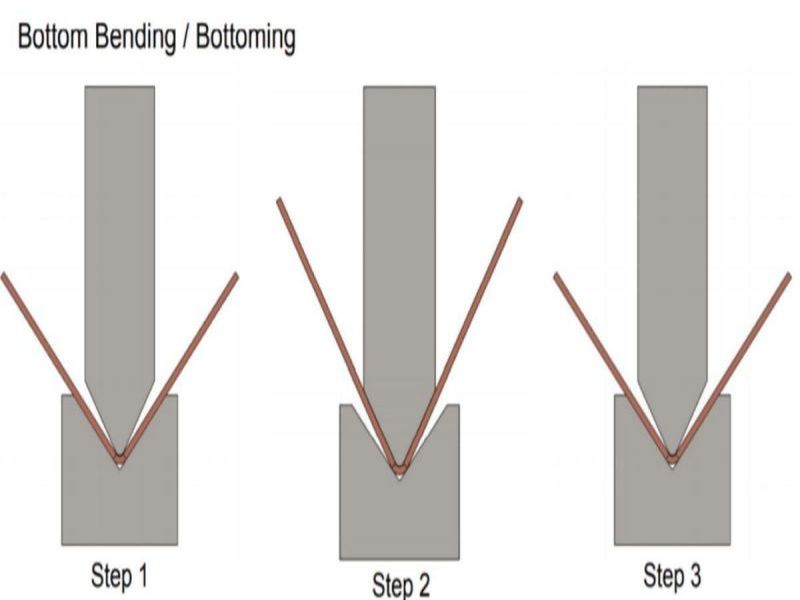
Hydraulic system failure
Description of the fault phenomenon: During the inspection and use of the hydraulic system, we found that the system could not generate enough pressure, or there was no pressure at all. The specific manifestation is that the hydraulic pump cannot work properly, resulting in the inability of the hydraulic oil to flow smoothly in the system, thereby being unable to provide sufficient power for the hydraulic cylinder or hydraulic motor. This situation may cause the device to malfunction or even stop working altogether. Further inspection revealed that the hydraulic system's pressure gauge was reading below the normal operating range, or was not reading at all, indicating a possible leak, blockage, or other mechanical failure within the system.
Possible cause analysis
- 1. The forward and reverse directions of the motor and pump are set incorrectly, which may cause the system to fail to work properly, thus affecting the normal operation of the equipment.
- 2. The valve core of the relief valve is blocked, which will affect the normal pressure regulation of the hydraulic system, causing the system to fail to work properly.
- 3. The valve core of the solenoid valve is blocked by foreign matter, which will cause the solenoid valve to be unable to open or close normally, affecting the system's normal operation.
- 4. There is a leakage problem inside the pressure control valve that cannot maintain the set pressure value, thus affecting the system's normal operation.
Solution suggestions
- 1. Carefully check the rotation direction of the motor and pump to ensure that it meets the system requirements to ensure normal operation of the equipment.
- 2. Thoroughly clean the valve core of the relief valve, remove blockages, and restore its normal pressure regulation function.
- 3. Clean the valve core of the solenoid valve and remove possible foreign matter to ensure that it can respond to the control signal normally and achieve accurate switching action.
- 4. Conduct a detailed inspection of the pressure control valve to find out the leakage point and repair it to ensure that it can maintain the set pressure value and ensure the stable operation of the system.
Fault phenomenon description
The slider descends slowly or is stuck.
Possible cause analysis
- 1. Cylinder wear or damage: Internal wear of the cylinder will affect the flow of hydraulic oil, causing the slider to move slowly.
- 2. Guide rails are worn or not vertical: Wear or non-vertical installation of the guide rails may cause the slider to run unsmoothly.
- 3. Low oil level in the oil tank: Insufficient hydraulic oil in the oil tank will affect the normal operation of the slider.
- 4. The rapid forward speed is too fast and the oil supply is insufficient: If the rapid forward speed is too fast, the oil supply of the hydraulic system may not be able to keep up.
- 5. The filling valve is stuck or not fully open: Failure of the filling valve will affect the pressure and oil flow of the hydraulic system.
Solution suggestions
- 1. Check the oil cylinder: Check the condition of the oil cylinder regularly and replace or repair it if necessary.
- 2. Check the guide rails: Ensure the verticality of the guide rails and lubricate and maintain them regularly.
- 3. Check oil level: Maintain the proper level of hydraulic oil in the tank.
- 4. Adjust the fast forward speed: Adjust the fast forward speed according to the actual situation to ensure sufficient fuel supply.
- 5. Clean the filling valve: Check and clean the filling valve regularly to ensure its normal operation.
Oil leakage in hydraulic system
Oil leakage occurs in the hydraulic system.
Possible cause analysis
- 1. Loose connecting screws and pipe joints: This will cause gaps in the connections, causing oil leakage.
- 2. Damaged seals: Damaged seals will cause hydraulic oil to leak out from the gaps.
Solution suggestions
- 1. Tighten screws and joints: Make sure all connections are tightened to avoid loosening.
- 2. Replace seals: Damaged seals need to be replaced in time to prevent hydraulic oil leakage.
Bending imbalance phenomenon
Unbalanced bending on both sides.
Possible cause analysis
- 1. Uneven wear of the mold: Uneven wear of the mold will lead to inconsistent bending on both sides.
- 2. Non-parallel slider: Non-parallel slider will lead to uneven bending force, resulting in unbalanced bending.
Solution suggestions
- 1. Adjust the hexagonal tube to correct the angle difference: By adjusting the hexagonal tube, the angle difference of the mold can be corrected to make both sides bend evenly.
- 2. Use the eccentric sleeve to adjust the parallelism: By using the eccentric sleeve, the parallelism of the slider can be adjusted to ensure uniform bending force.
Mechanical and electrical failure phenomena
Loud noise or electrical failure.
Possible cause analysis
- 1. Loose connections, worn bearings or damaged parts: These factors can cause noise when the equipment is running.
- 2. Loose wiring, faulty sensors, damaged circuits: These electrical problems can cause electrical failures.
Solution suggestions
- 1. Adjust the slider and replace the mold if necessary: Noise can be reduced by adjusting the slider or replacing the worn mold.
- 2. Check the wiring and replace the sensor or circuit if necessary: Electrical problems can be solved by checking and repairing the wiring and replacing damaged sensors or circuits.
Temperature and speed problems
Overheating or the slider cannot descend slowly and the bending force is weak.
Possible cause analysis
- 1. Radiator blockage, cooling system failure: These factors can cause the equipment to overheat.
- 2. 4/2-way valve failure, filling valve stuck: These hydraulic system problems will cause the slider to be unable to descend slowly and have weak bending force.
Solution suggestions
- 1. Clean the radiator and repair the cooling system: Overheating problems can be solved by cleaning the radiator and repairing the cooling system.
- 2. Check the 4/2-way valve and clean the filling valve: By checking and repairing the 4/2-way valve and the filling valve, the problem that the slider cannot descend slowly and the bending force is weak can be solved.
Conclusion
Summarizes common faults and the importance of maintenance, provides recommendations for preventive maintenance, and encourages readers to regularly inspect and maintain the press brake to ensure its normal operation. Through regular inspection and maintenance, potential problems can be discovered and solved in time, avoiding equipment failures, extending the service life of equipment, and ensuring production efficiency and product quality.
About Us
Durmapress specializes in designing, manufacturing and selling various metal processing equipment, including bending machines, shears, punches, laser cutting machines, etc. The company was founded in 2000. With years of experience and technology accumulation. DurmaPress has become one of the well-known brands in China's metal processing machinery industry.
Contact Us
Recent Posts
Categories
Follow Us
Weekly New Video
Contact us for more information
If you have any information about our products, please contact us and we will reply within 24 hours.