Analysis of the current status of bending technology in sheet metal industry
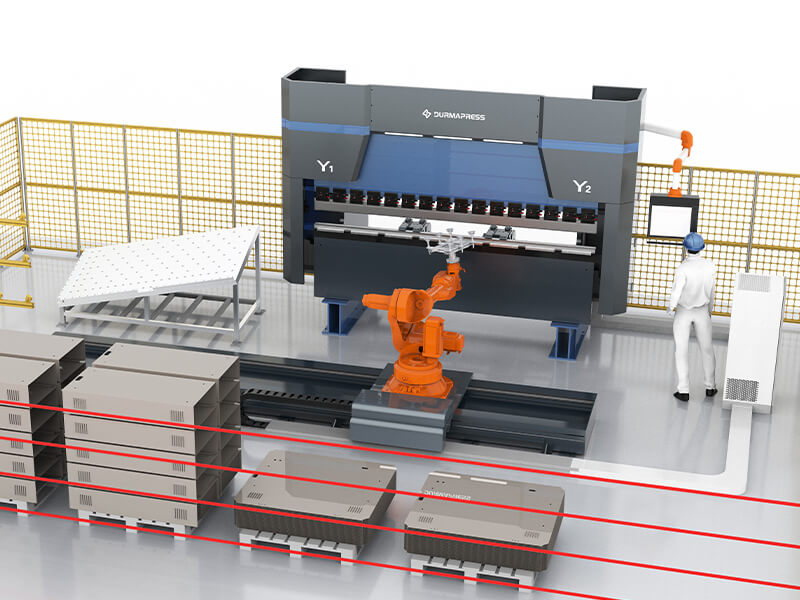
At present, intelligent and flexible processing technology has become the pursuit and desire of high-end sheet metal manufacturers. Therefore, the robot bending unit came into being in this market environment.In the sheet metal industry, most companies are still engaged in traditional bending processes. In the production process, due to the variety, specifications, and small batches of products, multiple bending machines and a large number of skilled and experienced sheet metal bending operators are still needed to complete the bending of workpieces. However, there are the following problems in actual work: First, due to the long working hours of operators, the endurance is not continuous, resulting in inconsistent height positions of the workpieces placed each time; second, the operators will not work stably like robots, so the bending workpieces are affected by manual labor, and the size and bending accuracy cannot be guaranteed, resulting in poor quality of finished products; third, facing large workpieces, generally 3-4 operators are required to complete the handling and operation, and the difficulty of recruiting workers and high costs are the difficulties of enterprises; fourth, the operator's work safety is poor, and there are great safety hazards when lifting the workpiece to work, which is prone to work-related accidents.
Nowadays, although the manufacturing and precision of sheet metal equipment bending machines have been greatly improved compared with the past, there is still a large gap with the current requirements for intelligent manufacturing. In terms of "intelligent production, personalized customization, service extension, and networked collaboration", it still requires joint innovation and development of sheet metal equipment manufacturing sub-sectors and demanders. This kind of innovation, development promotion, and application is another improvement and liberation of productivity.
Problems that need to be solved in traditional bending in the sheet metal industry
The traditional bending in the sheet metal industry needs to solve the following problems: (1) It cannot achieve multiple varieties, small batches, and fast switching; (2) The bending processing accuracy of high-precision workpieces in the sheet metal industry is low and the quality is unstable; (3) Sheet metal bending operators are scarce and the labor intensity of workers is high; (4) Personnel costs, safety hazards, process layout, and management operations.
Technical features of robot bending cell
1.Design and development
Design and development focuses on the characteristics of user personalized needs and customization, taking customer needs and goals as the priority, and conducting detailed technical exchanges with customers in the formulation of each technical solution; second, conducting computer simulation analysis on the workpiece processing drawings provided by customers; third, conducting on-site proofing tests on customers' typical workpieces; fourth, conducting classification analysis and data processing on customers' workpieces. After confirming that the above procedural work is completed, the technical solution will be formulated, and after the technical solution and solution drawings are approved by the customer, a comprehensive design will be carried out.The design of the robot bending unit aims to use the latest technology to realize the concept of intelligent products, so as to carry out real-time data exchange, real-time compensation and bending tracking in the production process. The main problems solved and the effects obtained are: (1) Solved the process difficulties of customized sheet metal production, and solved the problem of rapid switching production of multi-product, small batch and multi-variety parts in the elevator industry. (2) Solved the problems of unstable product quality, low part precision and poor product consistency. (3) Solved the problems of low production efficiency, unreasonable production layout and process route. (4) Solved the problems of difficulty in recruiting workers, high labor costs and high labor intensity of manual bending. (5) Improved the bending accuracy and automation level, improved the company's intelligent manufacturing capabilities, and improved the visual effect of customer visits.
2.Unique rack structure
Traditional bending machines generally use welded frames, including left and right columns, lower crossbeam (worktable), oil tank and supporting square beams, which adopt an integral welded structure. Its structural features: (1) ensure that the machine has no welding stress deformation; (2) improve the assembly accuracy of the machine; (3) increase the service life of the machine; (4) greatly improve the hydraulic compensation accuracy.
3.Sensor technology
In order to ensure high-precision sheet metal bending, sensors are installed on the upper beam (slider) and lower beam (workbench) of the bending machine. When in a working state, the deformation of the upper and lower beams is fed back to the CNC system (PC) in real time and accurately. After calculation and comparison, the CNC system outputs the corresponding compensation value to drive the compensation cylinder for dynamic compensation to obtain satisfactory part accuracy.
Laser Angle Measurement Technology
The AMS angle measurement system uses a closed-loop laser angle online measurement system. During the robot's automatic bending process, the AMS automatic application and the automatic angle measurement system with a built-in laser angle measurement device work together with the G-CS system to ensure the accuracy of the bending angle. Its main features are: (1) The bending angle after the workpiece rebounds is detected online by laser; (2) The force detection system automatically calculates the bending rebound amount; (3) The depth of the workpiece can be automatically adjusted according to the width of the lower die; (4) The closed-loop laser angle online measurement system ensures that the bending yield rate reaches more than 99.5%.
Robot automatically changes gripper and mold
Automatic gripper and die change by robots is a completely intelligent and automated operation method in the sheet metal field. This method consists of automatic die change software, robots and die library. When the automatic die change system is selected, the precision bending center can now automatically and randomly bend small batches of different products. With the automatic die change function, the die in the bending machine is no longer a limiting factor, and parts can be handled unmanned throughout the process. The gripper of the robot automatic mechanical device changes the die very quickly and is ready to bend the next batch of parts at any time.
1.Automatic mold changing software
The main features of the automatic mold change software are: (1) Through the attached graphical interface, the user can immediately see the current status of the entire system; on the right side of the interface, there is a graphic representation of the mold status, which divides the current position of these molds. (2) The entire interface includes the bending upper mold area, the bending lower mold area and the mold library; the display of the mold follows the size of the mold itself and the position of the clamped workstation. (3) The upper and lower molds are distinguished by different colors; on the upper left side of the interface, there is a detailed description of the mold installed on the bending machine. Two parts: one is to explain the upper mold, and the other is to explain the lower mold, describing the clamped mold by identification code and current position.
2.Management features
Press the icons of mold management, product management, mold library management, mold setting management, etc., and a corresponding window will pop up to set or manage related tasks.Press the settings icon to open the management settings box. Note: If a robot automatic mold change system is used, the mold is equipped with a dedicated mold change interface and a dedicated mold library.
CNC Sequential Bending Technology
CNC sequential bending technology is a high-precision bending control system suitable for workpiece shape and position tolerance processing. The device consists of a set of two sets of CNC front pusher operation systems with tracks. The displacement is transmitted and fed back by sensors. The entire operation is controlled by the CNC system. The control axis consists of X3\X4 and Z3\Z4. By configuring the CNC front pusher with displacement and the rear block for bending, even if the workpiece blanking size reaches ±1mm, it can easily ensure that the key size is within the controllable error, thereby improving the accuracy and efficiency of the parts.
Software and Control
Parametric programming software, offline programming software, and production management software are applied in the robot bending unit. At the same time, the bending follow-up, automatic mold change, automatic gripper change, flexible stacking, real-time compensation, plate edge search, flexible flip technology and bus control technology are developed. It can greatly meet the technical and software requirements of sheet metal bending for various customers. With the improvement of the overall level of China's machinery industry, the sheet metal manufacturing industry will have a new level of requirements for production equipment. In the end, the equipment that can solve problems for users will be favored by users.
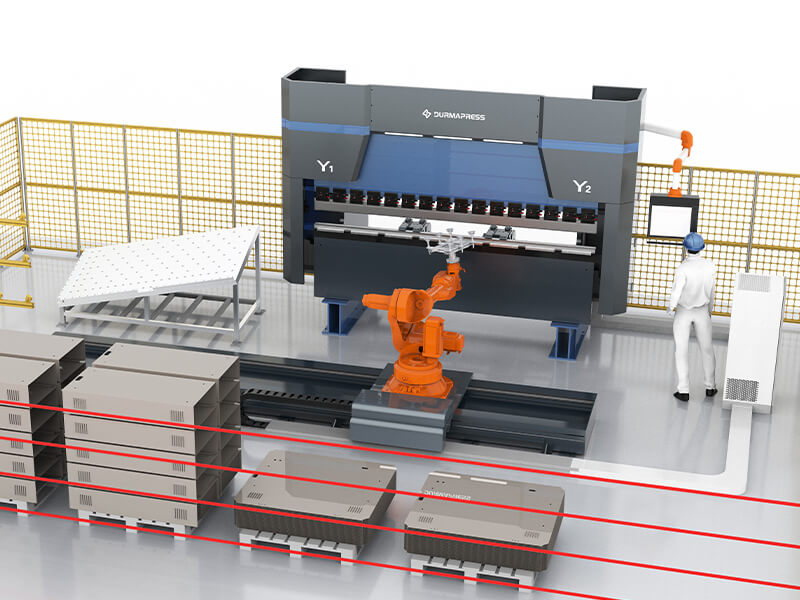
About Us
Durmapress specializes in designing, manufacturing and selling various metal processing equipment, including bending machines, shears, punches, laser cutting machines, etc. The company was founded in 2000. With years of experience and technology accumulation. DurmaPress has become one of the well-known brands in China's metal processing machinery industry.
Contact Us
Recent Posts
Categories
Follow Us
Weekly New Video
Contact us for more information
If you have any information about our products, please contact us and we will reply within 24 hours.