introduction
In modern industrial production,press brake plays a vital role as a key metal processing equipment. It is capable of precisely bending metal sheets according to predetermined angles and shapes, and is widely used in many fields such as automobile manufacturing, aerospace, shipbuilding, building decoration and so on. The emergence of thepress brake has greatly improved the efficiency and precision of metal processing, making it possible to produce metal parts of complex shapes, thus promoting the development of the entire manufacturing industry.
In the process of usingpress brakes for metal processing, the adjustment of fixtures is a link that should not be ignored. The role of the fixture is to fix and position the workpiece to ensure that the workpiece does not move or deform during the bending process, thus ensuring the accuracy and repeatability of the process. A well-designed and adjusted fixture can not only improve the processing efficiency, but also significantly improve the processing quality and reduce the scrap rate. Therefore, the accuracy of fixture adjustment is critical to achieving high-quality, efficient metal machining.
In order to utilize the full potential of apress brake, operators must have an in-depth understanding and knowledge of the principles and methods of fixture adjustment. This includes an understanding of the physical characteristics of sheet metal of different materials and thicknesses when bending, and how to select the appropriate fixture and adjustment parameters based on these characteristics. In addition, with the advancement of technology, modernpress brakes are often equipped with advanced CNC systems and automation functions, which requires operators to not only have mechanical operation skills, but also be able to skillfully use the relevant software and control systems.
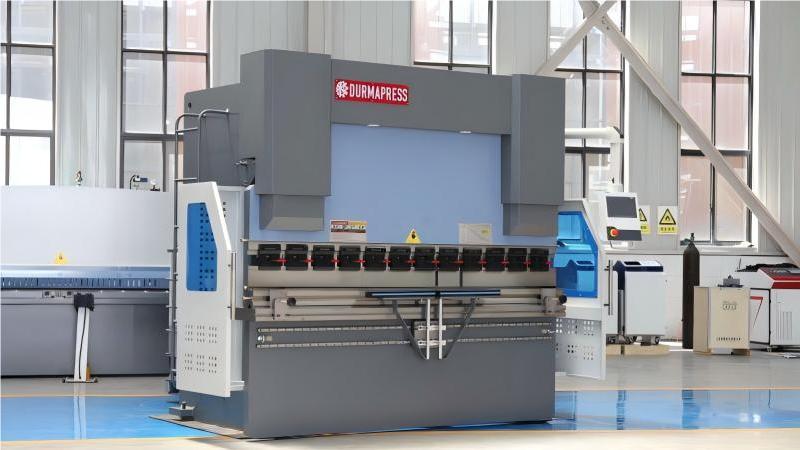
The role of the press brake fixture
Clamping the function of the upper tool of the mold
In modern industrial production,press brake plays a vital role as a key metal processing equipment. It is capable of precisely bending metal sheets according to predetermined angles and shapes, and is widely used in many fields such as automobile manufacturing, aerospace, shipbuilding, building decoration and so on. The emergence of thepress brake has greatly improved the efficiency and precision of metal processing, making it possible to produce metal parts of complex shapes, thus promoting the development of the entire manufacturing industry.
In the process of usingpress brakes for metal processing, the adjustment of fixtures is a link that should not be ignored. The role of the fixture is to fix and position the workpiece to ensure that the workpiece does not move or deform during the bending process, thus ensuring the accuracy and repeatability of the process. A well-designed and adjusted fixture can not only improve the processing efficiency, but also significantly improve the processing quality and reduce the scrap rate. Therefore, the accuracy of fixture adjustment is critical to achieving high-quality, efficient metal machining.
In order to utilize the full potential of apress brake, operators must have an in-depth understanding and knowledge of the principles and methods of fixture adjustment. This includes an understanding of the physical characteristics of sheet metal of different materials and thicknesses when bending, and how to select the appropriate fixture and adjustment parameters based on these characteristics. In addition, with the advancement of technology, modernpress brakes are often equipped with advanced CNC systems and automation functions, which requires operators to not only have mechanical operation skills, but also be able to skillfully use the relevant software and control systems.
Guaranteeing the stability of the mold during the bending process
The role of thepress brake fixture is not only limited to the function of clamping the tool on the mold, it also includes in the machining process, through the clamping mold to fix and position the tool to ensure that the tool can accurately carry out cutting, engraving or other processing operations. This function is critical to ensure machining accuracy and improve machining efficiency. Clamping dies are often designed with a precision positioning system that adjusts the position and angle of the tool to meet machining requirements, enabling accurate machining of the workpiece. In addition, the function of the clamping mold tooling includes providing sufficient stability during machining to prevent the tool from deviating from its intended trajectory due to vibration or external forces, ensuring smooth surfaces and dimensional accuracy. With this function, tool life can be effectively extended and downtime due to tool wear or damage can be reduced, thus increasing productivity and economic efficiency.
In the bending process, it is crucial to safeguard the stability of the mold. The stability of the mold directly affects the accuracy of the bending angle and the consistency of the shape of the workpiece. If the mold moves or deforms during the bending process, it will lead to deviations in the size and shape of the workpiece, thus affecting the quality of the product. Therefore, to ensure the stability of the mold in the bending process is an important prerequisite to achieve accurate bending angle and shape.
The importance of realizing accurate bending angle and shape
The importance of fixture adjustment
In metalworking, precise bending angles and shapes are critical to ensuring that the final product is of high quality and meets design specifications. Accurate
Points to note when adjusting fixtures
Ensuring fixture parallelism is a critical step in accurate bending. The bottom surface of the fixture must be aligned with the vertical plane of the table to avoid machining errors caused by tilting or misalignment of the fixture. The parallelism of the fixture directly affects the bending accuracy. Unparallel fixtures may lead to uneven stresses in the material during the bending process, thus affecting the angle and shape of the final product. Therefore, ensuring the parallelism of the fixtures is crucial to realizing high-precision bending.
The positional accuracy of the fixture is also critical to ensure the quality of the process. The exact position of the fixture on the table must be set accurately according to the design requirements to ensure proper alignment of the material. Positional deviations can lead to inaccuracies in the bending angle, affecting the size and shape of the product.
The use of measuring tools and methods of calibrating fixtures can help ensure parallelism and positional accuracy. Commonly used tools include calipers, levels and laser range finders, which can be used to accurately measure the parallelism and position of fixtures. Regular calibration of fixtures to detect and correct fixture deviations in a timely manner can help maintain machining stability and reliability. Through these methods, the accuracy and efficiency of the production process can be effectively improved.
Points to note when adjusting fixtures
Ensuring fixture parallelism is a critical step in accurate bending. The bottom surface of the fixture must be aligned with the vertical plane of the table to avoid machining errors caused by tilting or misalignment of the fixture. The parallelism of the fixture directly affects the bending accuracy. Unparallel fixtures may lead to uneven stresses in the material during the bending process, thus affecting the angle and shape of the final product. Therefore, ensuring the parallelism of the fixtures is crucial to realizing high-precision bending.
The positional accuracy of the fixture is also critical to ensure the quality of the process. The exact position of the fixture on the table must be set accurately according to the design requirements to ensure proper alignment of the material. Positional deviations can lead to inaccuracies in the bending angle, affecting the size and shape of the product.
The use of measuring tools and methods of calibrating fixtures can help ensure parallelism and positional accuracy. Commonly used tools include calipers, levels and laser range finders, which can be used to accurately measure the parallelism and position of fixtures. Regular calibration of fixtures to detect and correct fixture deviations in a timely manner can help maintain machining stability and reliability. Through these methods, the accuracy and efficiency of the production process can be effectively improved.
press brake fixture adjustment steps
Specific fixture adjustment steps include the following: First, mark the center vertical position of the workpiece, which helps to ensure the accuracy of the fixture mounting and adjustment position. Next, use an angle ruler to measure the angle of each point to ensure that the parallelism and positional accuracy of the fixture meets the requirements. If any errors are found, they need to be corrected by adjusting the fixture set screws. This process may need to be repeated to ensure that the fixture's accuracy is optimized to ensure the accuracy of the process and the quality of the product. The most important thing is to tighten the screws to complete the adjustment. By following these steps, machining safety and accuracy can be effectively improved.
Inspection and maintenance after adjustment
During metal machining, trial machining and measurement and inspection are critical steps to ensure the accuracy of fixture adjustments. Trial machining verifies that the fixture setup meets the design requirements, and measurement checking confirms that the accuracy of the bending angle and shape is up to standard. Regular maintenance and servicing of fixtures is essential to maintain machining quality and equipment performance. Regularly checking the fixtures for wear and tear can identify and fix potential problems in time to avoid machining errors caused by wear and tear. In addition, cleaning debris from the fixture is an important part of the maintenance process. Debris can interfere with the proper functioning of the fixture and lead to inaccurate machining. Keeping fixtures clean and in good condition will help improve machining efficiency and the quality of the final product.
Conclusion
The fineness and importance of fixture adjustment cannot be ignored, and accurate adjustment directly affects the final result of machining. Correct fixture adjustment not only ensures the accuracy of each bending, but also improves productivity and product quality. This process requires operators with the experience and expertise to accurately recognize and resolve potential adjustment problems. Experienced operators are able to optimize fixture operation through careful adjustment and calibration to maximize process performance, quality and efficiency. Accurate fixture adjustment is the foundation for achieving high standards of production and maintaining a competitive edge, and it plays a vital role in improving product consistency and reducing scrap rates.
About Us
Durmapress specializes in designing, manufacturing and selling various metal processing equipment, including bending machines, shears, punches, laser cutting machines, etc. The company was founded in 2000. With years of experience and technology accumulation. DurmaPress has become one of the well-known brands in China's metal processing machinery industry.
Contact Us
Recent Posts
Categories
Follow Us
Weekly New Video
Contact us for more information
If you have any information about our products, please contact us and we will reply within 24 hours.