LaserCheck Angle Measurement System
Solution / LaserCheck Angle Measurement System
Lasercheck For Press Brake
Manufacturing sheet metal parts with accurate bending angles that are kept constant all times often meets a problem during the actual production process: different parameters in material thickness and stresses. In order to solve this problem and to make use also of minor quality materials safe for the user, data M Engineering has developed a powerful solution for measuring bending angles in press brakes - the LaserCheck. LaserCheck enables the user to determine the exact bending angle for press brakes by using laser triangulation together with strain gauges - and it works contactless.
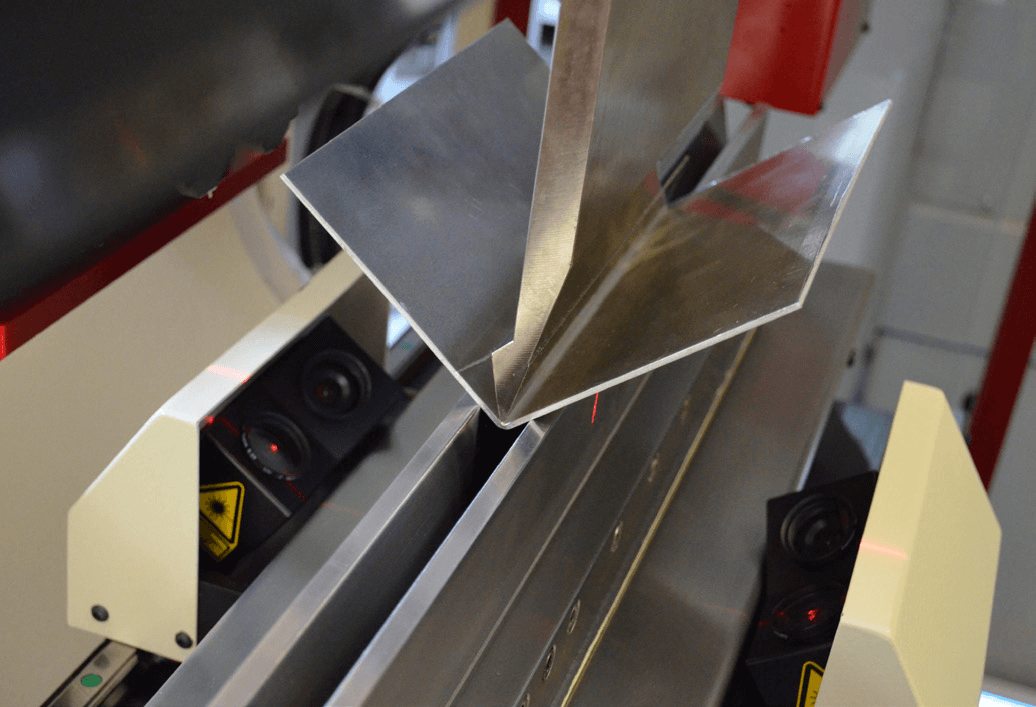
Watch the Video
LaserCheck-Bending Angle Measurement System
The sensor accuracy is better than ±0.1°. The bending accuracy is influenced by the control, the machine accuracy, the tools and the material. Bending accuracies of ± 0.3° are typically achieved. To increase the bending accuracy the sensors can be calibrated after mounting, so the mounting tolerance is reduced.
All sensors are pre-calibrated in order to work with reasonable results also without calibration. Only the mounting angle must be defined. Linear error corrections can be input for different measuring situations by the machine user.
LaserCheck 10
- Die width [mm]: from V6 to V60
- Die height [mm]: from 55 to 85
- Stand-off distance[mm]: 90-220
- Mounting angle: 55°
- Cable lengths: max. 5m (machine length max. 3m)
- Measurement range: 30°-180°
- Typical scan rate: 20 Hz
- Precision of sensor: ±0.2°
- Camera Interface: USB 2.0
- Optical class: 1/2“-CMOS
- Resolution (h x v): 1280x1024 (1,3 MP)
- Input voltage | Power: 5 VDC | 500mA via USB
LaserCheck 11
- Die width [mm]: from V6 to V100
- Die height [mm]: from 55 to 85
- Stand-off distance[mm]: 90-220
- Mounting angle: 45° ±10°
- Cable lengths: max. 50m
- Measurement range: 30°-180°
- Typical scan rate: 50-100 Hz
- Precision of sensor: better than ±0.1°
- Camera Interface: Gbit Ethernet (1 Gbit/sec)
- Optical class: 1/1.8“-CMOS
- Resolution (h x v): 1280x1024 (1,3 MP)
- Inputs: Trigger-Signal
- Input voltage | Power: 24 VDC | 90mA
LaserCheck 12
- Die width [mm]: from V6 to V100
- Die height [mm]: from 55 to 85
- Stand-off distance[mm]: 165-380
- Mounting angle: 45° ±10°
- Cable lengths: max. 50m
- Measurement range: 30°-180°
- Typical scan rate: 50-100 Hz
- Precision of sensor: better than ±0.1°
- Camera Interface: Gbit Ethernet (1 Gbit/sec)
- Optical class: 1/1.8“-CMOS
- Resolution (h x v): 1280x1024 (1,3 MP)
- Inputs: Trigger-Signal
- Input voltage | Power: 24 VDC | 90mA
Why LaserCheck?
LaserCheck is a comprehensive system designed for press brakes, featuring angle measurement sensors, various interfaces for press brake controllers, strain gauge sensors to detect spring-back, and motorized systems for sensor movements.
- Proven technology: The separation of sensors and CPUs enables cost-effective solutions for controls that support the LaserCheck software (Cybelec and ESA controls).
- Long-term support for all components.
- Bending angle correction during the bending process ensures perfect results from the first bend.
- Global setup support and training available worldwide or in-house.
Accessoires Of Lasercheck
Options
Sensors
For measuring from the punch with long working distance up to 2000mm (LaserCheck XR)
Longitudinal Adjustment
Necessary for different measuring stations. With servo- or stepping-motors with inductive proximity switch (fully wired and parametrised)
Range Extender WRE
For LaserCheck 11 und 12 necessary for large die width
Range Extender DRE
For LaserCheck 11 and 12 necessary for large tool heights
Contact us
High Tech Industrial , Bowang Town, Maanshan, Anhui, China
7/24