This article introduces the MES unmanned factory solution for laser processing, focusing mainly on the functions of the MES system, the pain points it solves, and its seamless integration with laser cutting machines. The entire article emphasizes the importance of integrating laser cutting machines, laser magic boxes, and MES systems to achieve digital, automated, and intelligent production, thereby enhancing the competitiveness of the factory.
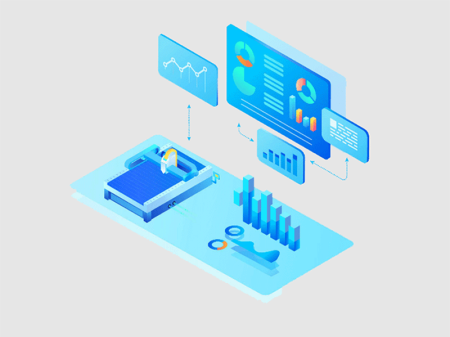
What is MES?
MES system, or Manufacturing Execution System, is an information system used to manage and monitor the production process. Positioned between Enterprise Resource Planning (ERP) systems and factory control systems, MES serves as a production management and collaboration software to manage, coordinate, and optimize production processes, promoting automation and transparency in workshop production and effectively enhancing the delivery capability of enterprises.
What Pain Points Does MES Resolve?
1.Improved Conversion Rate
MES systems help enterprises predict production times and delivery dates more accurately, enhancing the proportion of on-time deliveries. Timely delivery is key to increasing customer satisfaction and loyalty and is crucial for improving conversion rates.
2.Increased Production Efficiency
MES monitors the status of production lines in real-time, allowing for timely adjustments in production planning and scheduling, reducing downtime, and enhancing production efficiency.
3.Reduced Production Costs
The MES system enables well-planned, well-managed processes, saving time and costs. It minimizes manual work, improves production efficiency, and optimizes processes like material picking, scheduling, production operations, and logistics procurement. It helps enterprises better manage production processes, optimize resource allocation, lower material costs, speed up development, and reduce equipment maintenance costs.
4.Reduced Personnel Errors and Operational Difficulty
The MES system can automatically collect and organize data from the production process, eliminating human operation and input errors, providing more accurate and reliable information, and reducing the occurrence of personnel errors.
MES System Function Analysis
1.Production Planning Management
Production planning management is one of the key functions of the MES system, covering the entire production lifecycle from order receipt to delivery completion. Through the MES system, enterprises can establish, adjust, and optimize production plans. The system can automatically schedule production based on order requirements, rationally arrange resources and personnel, and improve production efficiency and flexibility. Additionally, through real-time monitoring of the production process, the MES system can prompt timely adjustments and processing to ensure smooth production progress.
2.Material Management
Material management is another crucial function of the MES system, encompassing the entire material flow process from procurement to receipt, storage, dispatch, and shipping. The MES system can track the location and status of materials in real-time, accurately record the quantity and time of material storage and retrieval, and provide accuracy and traceability of materials. Accurate material management helps enterprises reduce inventory costs, avoid excessive procurement and stockpiling issues, and improve material utilization and supply chain efficiency.
3.Quality Control
Quality control is an indispensable part of the production process. The MES system integrates quality control functions to provide comprehensive quality monitoring and management. The system can automatically collect and analyze key quality data during production, promptly identifying and addressing quality issues. By setting reasonable quality inspection standards and steps, the MES system can provide real-time quality reports and statistical analyses, helping enterprises continuously improve production processes and product quality to meet customer requirements.
4.Data Analysis and Decision Support
Data analysis and decision support are one of the core functions of the MES system. By collecting, processing, and analyzing production data, it provides real-time data support and decision-making references for enterprise decision-makers. The MES system can transform vast amounts of production data into visual reports and charts, helping decision-makers quickly understand production conditions and make scientific decisions. Through historical data analysis, the system can also identify potential problems and improvement opportunities, providing suggestions for optimizing the production process and helping enterprises continually enhance production efficiency and quality.
How to Better Integrate Laser Cutting Machines into a Digital Production Line with MES?
The rise of smart manufacturing has driven the integration of industrial equipment with information technology, achieving efficient, flexible, and intelligent production processes. In realizing smart manufacturing, the integration of industrial equipment data collection with Manufacturing Execution Systems (MES) is crucial. For laser cutting machines, pairing them with smart devices like Raybox can accelerate the journey toward smart manufacturing. Raybox possesses edge computing capabilities, allowing it to process and filter collected raw data, extract key information, perform real-time calculations and analyses, and transmit collected data to MES through interfaces.
What is a RayBox?
Raybox is a smart device that integrates data collection, edge computing, and communication functionalities. It collects device data in real time for processing and transmission. Raybox is dedicated to enhancing the processing efficiency of sheet metal factories, providing instant value to users. It offers multidimensional statistical analysis of machine tools, external statistical output interfaces, and smart factory dashboard functions, providing real-time feedback on machine tool processing statistics. The laser RayBox interfaces with automated loading and unloading systems, allowing centralized control of multiple laser machine tools, unified processing task management, and automatic processing of multiple machine tools.
How Does Raybox Control Laser Machine Tools?
Raybox can seamlessly connect multiple laser machine tools with MES systems, uniformly receiving MES processing task instructions and processing drawings, and distributing them to different machine tools as per rules. It provides real-time feedback on the processing progress during the machining process, helping MES systems jointly control and handle multiple laser machine tools and ensuring rational distribution of processing tasks.
1.Operating Conditions
Hardware Conditions
I3-9100 CPU, 180W power supply, 8G DDR4 RAM, 1T hard disk, Two-year warranty
Network Environment
When using Raybox, it can operate on the internet or an internal local network, but it must be on the same network as the laser machine tools.
2.Operating Guide
- Download: After starting up, Raybox runs automatically, and users can download Raybox on their computer.
- Adding Lathe: Raybox will automatically scan machines in the local network, but manual binding is required for the first use. Machine tools can be identified by IP address or computer name, or by running Raybox software on the machine to check the machine's IP address.
- Lathe List: The list of machine tools running CypCut, TubePro, or HypCut systems in the local network is displayed, showing their basic status information and historical process records.
3.Task Management
Task management can be divided into two types: plane tasks and pipeline tasks. Plane tasks support CypCut and CypNest. Pipeline tasks support TubePro and TubesT.
To create a processing task, first upload nested files or part drawings, and then enter information such as quantity and materials. By default, all machine tools can see this task, and you can choose to specify online machine tools for processing. The supported file formats for plane tasks include extensions like lxd, lxds, dxf, nrp, nrp2, cps, and cps2. Pipeline tasks support file formats with extensions like zx, zzx, yxy, ctd, ctds, and jhb. Raybox implements automatic transmission of graphic files in smart factories. It has a large file storage and scheduling management function, with 1T of hard disk space, providing read-write services for processing drawings for CypCut, HpyCut, and TubePro. Layouts on CypNest and TubesT can be saved in Raybox. Cutting software can retrieve processing tasks and files from Raybox. Raybox provides a two-dimensional code recognition feature for each processing file. Cutting software uses a scanner to scan the two-dimensional code, automatically retrieving the processing file from Raybox for processing. You can check the processing status of the task at any time, and view the processing time, remaining processing time, and completion degree.
4.Connecting Cutting Software to RayBox
Raybox serves as an industrial internet-level smart hardware for the laser industry, enabling seamless integration between CypCut, CypNest, HypCut, TubePro, and MES software, providing automatic circulation and storage management of processing drawings. Here, let's talk about the CypCut plane-cutting software.
Cypcut is a powerful software designed for laser cutting machines using fiber lasers, used for cutting stainless steel, aluminum, carbon steel, copper, gold, silver, and other metal plates and tubes. Its features include:
Automatic optimization of imported graphics
When importing external files, the original graphics are automatically optimized.
Clear and concise process settings
After importing graphics, users can quickly set processes like lead-ins, micro-connections, compensation, etc., with batch modification functionality, allowing quick completion of the entire plate's process settings.
Flexible processing control bar
Supports floating coordinate systems and workpiece coordinate systems, meeting the requirements of flexible production and facilitating batch production.
Rich machine statistics
Provides timely and comprehensive statistics on the use of machine tools.
Accurate edge-seeking assistance
Supports photoelectric and capacitive edge-seeking, quickly correcting deviations in plate materials.
Dual drive deviation self-correction
Utilizes gantry synchronization functionality, correcting the deviation of dual drive axes each time it returns to the origin.
To connect to Raybox, simply open CYPCUT, create a new layout task, add parts, then perform layout sorting and other tasks, find RAYBOX to connect, and after connecting, you can see the created tasks on Raybox and click "Open" for processing.
5.Factory Data Visualization Screen
The real-time monitoring screen provided by Raybox offers multidimensional statistical analysis of machine tools, including processing statistics, daily processing reports, operational statistics, cutting length and stroke statistics, piercing count statistics, etc. Raybox provides an external statistical output interface and smart factory billboard functionality, changing the traditional method of manual statistical workload.
Customer Case Study
A large bathroom manufacturing enterprise manages every step from receiving orders to production, and finally to product storage, using an efficient Manufacturing Execution System (MES). However, the company's management found that despite the powerful capabilities of the MES, challenges remained in interfacing with certain key equipment. Particularly for laser cutting machines, which play a crucial role in sheet metal and metal bathroom manufacturing, the efficiency of these machines directly impacts the entire production line's rhythm. Any bottleneck can affect the whole production process.
An innovative solution, "RayBox," was discovered. This compact yet powerful device was introduced into the production line. The RayBox serves to connect the MES system with the laser cutting machines, allowing seamless communication. The MES system sends processing tasks to the laser cutting machines via the RayBox, also obtaining real-time information on task progress and processing duration. With this data, managers can better optimize production rhythms, reduce costs, and enhance the efficiency of the production line, achieving more refined management.
Additionally, the marking system can also communicate with the MES system through the RayBox. It can obtain identification information of the parts in the processing tasks and print labels on each part. Each part receives a unique barcode, making it easier to track and smoothly transition into the next process.
Ultimately, with the introduction of the Laser RayBox, the integration issues between the MES system and laser cutting machines were readily solved. The MES system can now monitor the operation of the laser cutting machines in real-time, effectively addressing the issue of laser cutters being "information islands" in the smart factory.
What are the Advantages of Using the RayBox?
By using Raybox for industrial equipment data collection and transmitting this data to MES through interfaces, enterprises can achieve the goal of smart manufacturing and gain the following advantages:
1.Integrated Data Collection and Edge Computing
Raybox can collect device data in real-time and process and transmit it at the device end, reducing data transmission volume and improving response speed.
2.Optimized Processing Efficiency
It provides multi-dimensional statistical analysis of machine tools and real-time feedback on machine processing statistics, helping to improve the processing efficiency of sheet metal factories.
3.Smart Factory Integration
Raybox supports seamless integration with MES systems, uniformly receiving processing task instructions and drawings, and enabling centralized control and task management for multiple laser machines.
4.Easy Operation
Users can easily download and operate Raybox on their computers. It supports automatic scanning of machines in the local network and displays basic status information and historical process records of machine tools.
5.Flexible Task Management
Raybox supports various types of tasks (such as flat and pipe tasks) and multiple file formats, allowing users to upload nested files or part drawings to create processing tasks.
6.Real-Time Monitoring and Feedback
It provides real-time monitoring screens, offering users processing statistics, daily reports, operational statistics, and smart factory billboard functionality, changing the traditional method of manual statistics. Real-time data collection and transmission help enterprises understand equipment status and production situations in time, aiding in optimizing production plans and adjusting production processes, improving production efficiency and product quality.
7.Software Compatibility
Raybox seamlessly integrates with various cutting software such as CypCut and TubePro, providing automatic circulation and storage management of processing drawings.
8.Enhanced Process Efficiency and Precision
With auxiliary features like edge-finding assistance and double-drive error self-correction, Raybox improves the precision and efficiency of processing.
How much to establish a laser cutting machine MES
MES factory is influenced by a variety of factors including the size of the factory, types of equipment, geographic location, labor costs, technological level, and other additional costs. Major expenses include the purchase of equipment (such as laser cutting machines, MES systems, RayBox,automation, and quality inspection equipment), investment in factory buildings and land, labor costs (encompassing salaries for various categories of staff), research and development and technical support, energy costs, as well as operating and maintenance expenses. Moreover, costs related to regulatory compliance, marketing and sales, financial and administrative expenses, insurance costs, as well as a contingency fund for unforeseen expenses and other miscellaneous costs should also be taken into account. The specific investment amount should be determined based on a detailed business plan, market demand, and economic conditions. If you have requirements in this area, please feel free to consult us!
Laser cutting machines + Laser RayBox + MES system, achieving seamless integration, truly meet the new requirements of laser cutting in the era of the Industrial Internet. This integration is a significant advancement for factories looking to achieve automated processing, real-time monitoring, task management, and MES integration for digitalization, automation, and intelligence. This integrated solution enhances the efficiency, visualization, and intelligence of the production process, bringing greater competitive advantages to enterprises.
About Us
Durmapress specializes in designing, manufacturing and selling various metal processing equipment, including bending machines, shears, punches, laser cutting machines, etc. The company was founded in 2000. With years of experience and technology accumulation. DurmaPress has become one of the well-known brands in China's metal processing machinery industry.
Contact Us
Recent Posts
Categories
Follow Us
Weekly New Video
Contact us for more information
If you have any information about our products, please contact us and we will reply within 24 hours.