Rules for selecting press brake tooling
Make sure the fixture is accurate
When choosing a press brake, the first step is to ensure that the fixture is accurate. Precision fixtures simplify the process by requiring little or no additional adjustment during setup. High-precision fixturing improves bending quality, reduces errors and ensures consistent results every time. This is especially important for high-volume production or operations that require high-precision bending. In addition, high-precision fixturing extends the life of the machine and reduces wear and tear caused by frequent adjustments. Therefore, when selecting a press brake, be sure to check the accuracy specifications of the fixtures and choose the one that will meet your production needs.
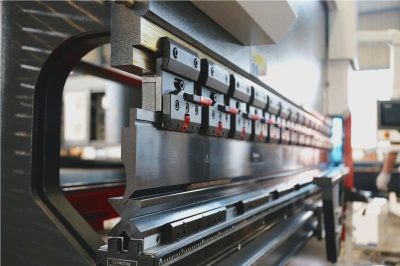
Note dimensions and tooling requirements
Checking the exact dimensions and tooling requirements before purchasing a press brake is an important step in ensuring you choose the right equipment. You need to know the dimensions of the metal to be processed, such as thickness, length and width, and select the right press brake based on these parameters. By providing accurate measurements, you can avoid having too much or not enough equipment, save money and increase productivity.
The three main types of press brake tooling systems
The type of press brake determines the type of tooling it is suitable for and how it operates. Below are the three main types of press brakes.
American Tooling System
The American Die System is known for its quick setup and ease of operation. Its punches are held in place by self-locating slots that align automatically at the push of a button, no special fixtures are required, and safety hooks aid in vertical loading and unloading. This system is suitable for environments that require frequent die changes and efficient production.
European style tooling system
Often sold with new press brakes, the European die system has limitations as an older die type. It comes with extendable punch holders, making it economical to use the force. This system is suitable for users who have a limited budget but still need reliable performance.
New Standard tooling System
The New Standard Die System combines old and new technologies to increase speed and accuracy with greater flexibility and is considered to be the most accurate system available. With the ability to adapt to a variety of complex machining needs, this system is ideal for high-end production environments.
Tooling Types
There are a variety of tooling types for press brakes, each with its own specific application scenario. Below are a few common types of tooling.
American Precision tooling
American precision tooling have a winged structure with a 0.500-inch wide joint and are compatible with laser press brakes and other safety systems. This type of tooling is known for its high precision and reliability for jobs that require highly accurate bending.
Diagonal Joint tooling
Designed for use with Amada style press brakes, the angled joint tooling has an angled joint that fits perfectly into the receiving fixture, facilitating faster and safer tooling changes. This tooling is ideal for quick tooling changes and efficient production environments.
European Style Precision tooling
The Euro Precision Die is 13 mm wide and has a rectangular slot on the side facing the operator, which enables it to interface with the receiver inside the press brake. It is suitable for bending operations that require high precision and stability.
Wila Trumpf Style tooling
The Wila Trumpf style die has a 20 mm wide joint with slots at the front and back, holding the punch by one or two mechanisms, and is suitable for narrow channels and making boxes. These tooling are known for their flexibility and versatility.
Large Weight tooling
Heavy weight tooling weighing over 27.6 lbs. usually have a small pin mounted on the side of the press brake to hold the heavy duty die in place for safety and stability.
Quick Change Button tooling
Weighing less than 27.6 lbs, Quick Change Button tooling have a spring loaded Quick Change Button that is easily mounted from the front of the press brake for production environments that require frequent die changes.
Various Types of tooling
Choosing the right tooling is critical to streamlining your operation. Here are some common types of tooling:
Rocker-Type tooling
Rocker-Type tooling bend inserted metal by sliding it up and down, left and right, and are suitable for multi-directional bending operations. The design of the Rocker-Type Die allows it to apply pressure in different directions to bend the sheet metal to a predetermined shape. Its unique sliding mechanism makes this type of die very effective when working with complex shapes. They are widely used in the fields of metalworking, machine building and tooling making, especially where complex shaped workpieces need to be handled.
Gooseneck tooling
Gooseneck tooling are used to clean up protruding edges on workpieces, also known as flanges, and are suitable for handling complex shaped workpieces. Gooseneck tooling are shaped like the neck of a goose, with curved and narrowed features. During processing, the workpiece is placed on the die and the protruding edges or flanges are removed by applying pressure.
V-Die
Used to make V-shaped bends, V-tooling are the most common type of bending die and are used in a wide range of applications.V-tooling work by placing sheet metal in the V-shaped grooves of the die and then applying pressure to bend it into a V-shape. Because of its simple yet effective design, the V-die is able to perform a variety of V-bending tasks quickly and accurately.
Sharp Angle tooling
Sharp angle tooling can produce bends at different angles, such as acute, obtuse and right angles, and are suitable for processing a wide range of angular requirements. Sharp angle tooling are flexible in design and can precisely control the bending angle to ensure the angular accuracy of the processed parts.
Seam tooling
Seam tooling are used to create seams in metal sheets and tubes, and are a relatively simple type of die for basic seaming operations. Seam tooling are easy to operate and can complete seam operations quickly with strong, beautiful seams. It is suitable for joining various metal sheets and tubes, and is widely used in the fields of home appliance manufacturing, machinery manufacturing and construction industry.
Multi-bending tooling
Multiple bending tooling can produce multiple shapes on metal sheets and are suitable for complex multiple bending operations. Multiple bending tooling are complex in design, but powerful enough to complete multiple bending steps at once, increasing productivity.
Crimping tooling
Crimp tooling are used to crimp and coil the edges of sheet metal, while offset tooling create Z-shaped pieces by demonstrating two angles and using a punch and die set for specific edge finishing needs. The crimping die allows for precise control of the degree and angle of crimping, ensuring the quality of the crimped edge of the sheet.
To summarize
press brake and die selection is a critical step in achieving efficient and accurate metal processing. Understanding the different types of press brake systems and tooling can help you make informed decisions about purchasing and using them to improve productivity and product quality. Whether it's a quick-setup American-style tooling system or a new standard tooling system that combines the advantages of both old and new technology, each type has its own unique advantages and application scenarios.
When selecting a specific tooling, it is important to consider its precision, durability and applicability. From American precision tooling to multiple bending tooling, each type of tooling can be adapted to meet specific processing needs. By carefully evaluating the requirements of your project and selecting the most suitable tooling, you can ensure that the results of each bending operation meet the desired standards. By following the rules and recommendations above, you can better plan and execute bending operations that not only increase productivity, but also ensure quality and consistency in the final product. Flexibility in applying this knowledge and skills to your future metalworking projects will help you stand out from the competition.
About Us
Durmapress specializes in designing, manufacturing and selling various metal processing equipment, including bending machines, shears, punches, laser cutting machines, etc. The company was founded in 2000. With years of experience and technology accumulation. DurmaPress has become one of the well-known brands in China's metal processing machinery industry.
Contact Us
Recent Posts
Categories
Follow Us
Weekly New Video
Contact us for more information
If you have any information about our products, please contact us and we will reply within 24 hours.