Among machine tools and equipment, I believe everyone is familiar with the shearing machine. It is a commonly used mechanical equipment that is mainly used for cutting, trimming, and shaping metal sheets. However, many people do not know much about its development history. Its history can be traced back to the early 18th century. As technology advanced and demand increased, shears gradually evolved into efficient and precise equipment.
What is a shearing machine?
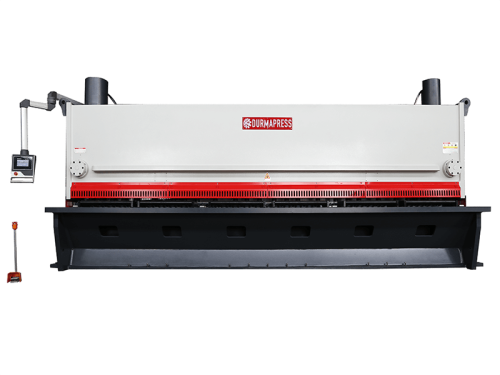
A shearing machine is a mechanical device that uses shearing action to cut metal sheets and coils. Its main components include an upper tool holder, lower tool holder, blade, auxiliary tool holder, hydraulic cylinder, driving mechanism, and control system. When working, place the metal material to be cut between the upper and lower tool holders, use a reasonable blade gap, and the hydraulic cylinder applies force to the blade to shear the material, so that the plate breaks and separates according to the required size to complete the cutting operation.
The shearing machine has the characteristics of a simple structure, convenient operation, and high cutting quality. It uses a hydraulic drive and multiple sets of blades to work together, which can effectively improve work efficiency and precision. At the same time, it is suitable for cutting various types of metal materials, such as ordinary steel plates, stainless steel plates, aluminum plates, carbide, etc.
Important stages in the development of shearing machines
First stage
Before industrialization, people used hand tools such as scissors, knives, and scissors to cut sheet metal. These methods are inefficient and unsuitable for large-scale production. From the end of the 18th century to the beginning of the 19th century, mechanical shearing technology initially developed. The scissor machines at that time mainly used human power or steam power to complete the shearing operation through the force acting on the lever. These machines increase shear speed but still rely on human labor.
Second stage
At the end of the 19th century, the introduction of hydraulic technology brought revolutionary changes to the development of shears. Early hydraulic shears used hydraulic cylinders to provide additional shear force, thereby increasing productivity and accuracy.
Third stage
At the beginning of the 20th century, the gradual maturity of electric drive technology promoted a new round of development of shearing machine tools. Electric shears use electric motors to drive scissors for shearing operations, which greatly improves work efficiency. These machines are powered by electric motors, making operation easier and more efficient.
Forth stage
In the 1980s, with the rapid development of computer technology, CNC technology began to be applied to the field of shearing machine tools. CNC shearing machines achieve high-precision and high-efficiency shearing operations through pre-programming, reducing tedious manual operations and improving processing quality and production efficiency.
Fifth stage
In recent years, the rapid development of laser technology has brought new breakthroughs to shearing machine tools. The laser shearing machine heats and shears metal sheets through laser beams. It has the characteristics of non-contact processing, high precision, and high speed, and is widely used in the high-precision metal sheet processing industry. The level of automation and intelligence of shearing machines continues to improve. The automated system can automatically load and unload materials, and the intelligent control system can adjust cutting parameters in real-time to optimize production efficiency.
Structure of Shearing Machine
The basic components of a shearing machine include the base, transmission system, guide rails, cutting tools, safety guards, and operating control system. The base serves as the supporting structure for the shearing machine, the transmission system transfers power from the motor to the cutting tools, and the guide rails ensure the proper movement of the cutting tools into position. Finally, the operating control system monitors and controls the operation of the shearing machine.
In practical operation, shearing machines are often optimized structurally to meet different processing requirements. For example, automatic clamping devices and digital control systems may be added to improve cutting efficiency and precision. Additionally, to ensure the safety of operators, shearing machines are typically equipped with safety guards and emergency stop buttons.
Common Classification of Shearing Machines
Classification by Operating Mode
Manual Shearing Machine
Manual shearing machines are typically operated by personnel who manually manipulate the cutting tools. Integrated servo systems can be applied to the cutting tool drive section of manual shearing machines to provide more precise control over tool positioning and force adjustment, enhancing cutting accuracy and efficiency. Manual shearing machines are suitable for simple cutting operations on thin sheets and thin profiles. However, they require a significant amount of manual labor and offer lower precision compared to other types of shearing machines.
In summary, manual shearing machines are valued for their simplicity of operation, ease of maintenance, low cost, and versatility. They find wide applications in manufacturing, maintenance, and on-site engineering scenarios.
CNC Shearing Machine
The CNC shearing machine is a high-precision shearing machine controlled by CNC technology. Equipped with imported servo motors and a high-precision hydraulic system, it is capable of high-speed and high-precision cutting.
This type of machine operates by executing digital commands issued by a CNC system. These digital commands are typically stored in a computer or a programmable logic controller (PLC). When different shapes of sheets need to be cut, operators simply input the corresponding digital commands into the computer or PLC, and the machine automatically carries out the cutting actions.
Furthermore, CNC shearing machines boast high precision, speed, and efficiency. Through advanced sensor technology, CNC shearing machines can continuously monitor the thickness, dimensions, and cutting quality of the sheets, enabling real-time adjustments and optimizations. They are suitable for industries with stringent requirements for precision and product quality, such as aerospace and automotive manufacturing.
Classification by Power Source
Mechanical Shearing Machine
Mechanical shearing machines are one of the earliest types of shearing machines and are primarily composed of a frame, cutting blades, cutting table, transmission system, and other components. The working principle involves the transmission system driving the upper cutting blade to press down on the metal sheet, exerting cutting force on the cutting table to separate the metal sheet into the desired shapes and sizes. Mechanical shearing machines have a simple structure and are relatively affordable. However, they offer lower cutting efficiency and are suitable for light-duty cutting applications. They still have a market demand in this particular niche.
Hydraulic Shearing Machine
The hydraulic shearing machine is a common type of shearing machine that utilizes a hydraulic system as its power source. It offers advantages such as high cutting force and a wide cutting range. Typically, it can handle sheet thicknesses ranging from 4 to 40mm and lengths between 2000 and 6000mm, making it suitable for cutting various types of metal materials. The hydraulic shearing machine operates by employing a movable upper blade and a fixed lower blade, using an appropriate blade gap to apply shearing force to metal sheets of different thicknesses, thus allowing for precise cutting to the desired dimensions.
The machine's operation involves oil entering the upper chamber of the left-end cylinder, causing the piston to descend. Simultaneously, oil from the lower chamber of the same cylinder enters the upper chamber of the right-end cylinder, resulting in its descent. This ensures parallel movement of the blade frame. By adjusting the oil flow in the series hydraulic circuit, the shearing angle of the blade frame can be varied. When shearing two copper sheets, reducing the shearing angle not only ensures that the material remains flat but also shortens the stroke of the blade frame, ultimately increasing the number of strokes per minute. In this configuration, a nitrogen accumulator is often used to drive one or two return cylinders to shorten the return time, thus enhancing the machine's productivity.
Hydraulic shearing machines can be further categorized into two types: hydraulic swing shearing machines and hydraulic guillotine shearing machines. Their respective fields of application determine their advantages and characteristics.
The swing shearing machine is powered by a hydraulic system, and it gets its name from its working principle. During the cutting process, the upper blade frame of the swing shearing machine swings around a fixed axis, allowing for arcuate motion. Lever action minimizes stress at the pivot point, thereby extending the cutting blade's lifespan and the overall machine's durability. This design is compact and provides infinite adjustment of the upper blade frame's stroke, significantly enhancing work efficiency.
The advantages of the swing shearing machine include its simple structure, ease of operation, high cutting precision, and high efficiency. It is suitable for cutting various metal materials, such as steel sheets, aluminum sheets, and copper sheets. Additionally, it can be customized to meet specific requirements, such as the installation of automatic feeding devices and CNC systems, further improving production efficiency and precision.
Hydraulic Guillotine Shearing Machine
The guillotine shearing machine utilizes a frame structure made of welded steel and features four-sided, right-angle guide rails for high precision and rigidity. It employs hydraulic pre-tightening of the guide rails. The hydraulic system uses two-way inserted integrated valves, and the entire system is controlled by a centralized button control panel. The guillotine shearing machine's upper slide and lower hydraulic cushion offer dual-action capabilities, with working pressure and stroke adjustable within specified ranges to meet process requirements.
The working principle involves the hydraulic system applying substantial pressure to move the upper blade downward, pressing it against the lower blade. When the pressure reaches the preset value, the upper and lower blades come into contact, generating significant shearing force to cut metal sheets or profiles to the required lengths. This process is repeated to achieve batch production.
The advantages of hydraulic guillotine shearing machines lie in their high efficiency, precision, and powerful shearing capabilities. With hydraulic drive and precise mechanical mechanisms, they deliver fast and accurate shearing while accommodating various metal sheet thicknesses and strengths. Additionally, their high degree of automation and user-friendly operation greatly enhance production efficiency.
Hydraulic guillotine shearing machines find widespread applications in metal processing, manufacturing, construction, and other industries. In metal processing, they are used for cutting various sheets and profiles, while in the manufacturing industry, they can cut steel beams and frames of different sizes. In the construction sector, they are employed to cut various types of reinforcement bars and steel plates.
Electric Shearing Machine
The electric shearing machine is a type of shearing machine that employs an electric motor to drive the downward movement of the upper cutting blade. Its structure is similar to that of a mechanical shearing machine and consists of a frame, motor, reducer, slide block, blades, emergency stop switch, and other components. The frame serves as the main structure of the equipment, with the blades mounted on it. The motor drives the slide block's movement through the reducer, causing the blades on the slide block to perform the cutting action. An emergency stop switch is used for immediate machine shutdown in case of emergencies.
The operation of an electric shearing machine is straightforward, offering high cutting efficiency. It is suitable for the processing of medium and small-sized metal sheets. Electric shearing machines are commonly found in various manufacturing, maintenance, and large-scale construction sites.
Working Principle of Shearing Machine
The working principle of a shearing machine involves several key components. The upper blade is fixed on the blade holder , while the lower blade is fixed on the lower bed The bed surface is equipped with support balls to facilitate the movement of the sheet metal being fed into the machine. A rear material stop plate is used for sheet metal positioning and can be adjusted using an adjustment pin . The hydraulic material clamping cylinder is employed to secure and prevent the sheet metal from flipping during the shearing process. The safety shield serves as a safety device to prevent workplace accidents.
(1) Adjustment of the Front Stop Plate
Position the rear material stop plate against the lower blade, then place a template against the rear stop plate.
Align and secure the front stop plate against the template.
Release the rear material stop plate, remove the template, load the sheet metal, and proceed with the shearing operation.
(2) Adjustment of the Rear Stop Plate
Place a template on the table, aligning it with the lower blade.
Secure the rear stop plate against the template.
Remove the template and load the sheet metal for shearing.
(3) Adjustment of the Angle Stop Plate
Start by placing the template on the table, and aligning it with the lower blade.
Adjust and secure the angle stop plate.
Adjust the rear stop plate according to the template during the shearing process. Utilize both the angle stop plate and rear stop plate for positioning.
Advancements and Trends in Shearing Machine Technology
Improved Precision
With the development of modern technology, the cutting precision of shearing machines has significantly improved. The application of precision sensors and intelligent control systems enables more accurate and stable cutting.
Automation
As control and sensor technologies advance, shearing machines are becoming more automated, with automation control of loading, unloading, and cutting processes. Automation technology allows shearing machines to automatically adjust cutting parameters, perform automated cutting, and handle waste material removal, greatly enhancing production efficiency.
Energy Efficiency and Environmental Friendliness
Design considerations for shearing machines increasingly prioritize energy conservation and environmental protection. These machines incorporate highly efficient and energy-saving drive systems, as well as tool designs that maximize material utilization, reducing resource waste and environmental pollution.
Versatility
Modern shearing machines can perform not only standard cutting tasks but also complex processes such as bending and stamping. This versatility widens the scope of shearing machine applications in various industrial fields.
Digitization and Intelligence
Leveraging artificial intelligence and internet technologies, shearing machines are becoming more intelligent and digitally connected. The introduction of digital technology enables data collection, remote monitoring, and machine learning capabilities, making shearing machines easier to maintain and manage.
How to Operate a Shearing Machine?
The operation process of a shearing machine mainly consists of machine preparation, workpiece clamping, shear adjustment, shearing processing, and workpiece release. Machine preparation involves checking the equipment to ensure that all its components are functioning correctly. Workpiece clamping is the process of securely fastening the metal sheet to the machine's worktable and adjusting its position and tension. Shear adjustment requires making relevant adjustments and corrections based on factors such as workpiece thickness, length, and shear angle. Shearing processing involves initiating the shearing machine to perform the cutting operation and complete the machining task. Workpiece release entails removing the finished metal sheet from the machine and cleaning the shear blades and worktable. The specific operating steps are as follows:
- Before starting, operators should wear tight-fitting protective clothing, secure cuffs, and ensure that clothing is not loose or open at the bottom. Do not change clothes near operating machinery, and avoid wearing skirts or slippers.
- A designated person must be responsible for managing the shearing machine.
- Machine operators must be familiar with the main structure, performance, and usage of the shearing machine.
- The shearing machine is suitable for cutting various steel plates, copper plates, aluminum plates, and non-metallic materials with a thickness equal to the machine's rated value. The materials should be free from hard marks, slag, inclusion, or welding seams, and the thickness should not be exceeded.
- The usage steps of the shearing machine are as follows:
a. Adjust the blade clearance according to the thickness of the material to be cut.
b. Adjust the back gauge or fixture according to the width of the material to be cut.
c. Before operating the machine, perform 1-3 empty cycles to ensure normal operation. - If any abnormality is observed during operation, immediately cut off the power and stop the machine for inspection.
- When adjusting the machine, the power supply must be disconnected, and caution should be exercised when handling the work piece.
- Regularly lubricate all parts of the machine, with the operator adding lubricating oil once per shift, and a maintenance worker adding lubricating oil to the rolling bearings every six months.
- During operation, coordinate hand and foot movements, avoid wearing gloves, and never insert hands into the clamping or cutting area.
- When multiple operators work together, a designated person must coordinate the operation. Simultaneous cutting of two pieces of material on the same shearing bed is strictly prohibited.
- Maintain a clean work environment, avoid cluttering work pieces and debris, and ensure the shearing machine and the surrounding area are clean.
- After work, cut off the power and lock the power box.
Maintenance and Care
- Follow the operation guidelines strictly.
- Add lubricating oil at scheduled intervals, locations, and quantities before each startup, ensuring clean and sediment-free oil.
- Keep the shearing machine clean regularly, and apply rust-prevention grease to unpainted areas.
- Check the working conditions and safety of electrical components frequently.
- Periodically inspect and replace damaged components like V-belts, handles, knobs, buttons, and keep spare parts in stock.
- Ensure that the emergency stop switch, fuses, handles, and switches are in good working order.
- Lubricate and clean the machine daily for the last 10 minutes of work.
- Unauthorized personnel are strictly prohibited from operating the equipment, and it is essential to ensure that the machine is stopped when people are not present.
Applications of Shearing Machines in Industries
- Manufacturing: Shearing machines are vital tools in the manufacturing industry, used for cutting and processing various metal materials, including steel sheets, aluminum sheets, stainless steel sheets, and more. These materials are often used in the production of components, parts, machinery, and industrial products.
- Construction: In the construction industry, shearing machines are used to cut rebars, metal sheets, and pipes to meet the requirements of structural and concrete projects. They are also used in the manufacturing and processing of metal components for construction.
- Automotive Manufacturing: The automotive industry utilizes shearing machines to cut and process metal materials for producing components such as car body panels and chassis parts.
- Shipbuilding: Shearing machines are used in shipbuilding for cutting and fabricating components of ships, including hulls, cabins, and bridges.
- Aerospace Industry: The aerospace sector demands high-precision metal components, and shearing machines are used to cut and manufacture components for aircraft, rockets, satellites, and other aerospace products.
- Metal Fabrication: Metal fabrication companies use shearing machines to process metal materials, producing various products such as furniture, appliances, and gas appliances.
- Steel Industry: In the steel industry, shearing machines are employed for processing and cutting steel materials to manufacture various types of steel products.
- Metal Recycling: Shearing machines play a critical role in the scrap metal recycling industry, cutting and shearing scrap materials into manageable pieces for processing and reuse.
- Pipe Manufacturing and Installation: Shearing machines are used to cut and process pipes to meet the requirements of pipe manufacturing and installation projects.
- Custom Manufacturing: Shearing machines are widely used in custom manufacturing, producing metal components of specific specifications and shapes based on customer requirements.
Applications are found in various industries such as light industry, aviation, shipping, metallurgy, instrumentation, electrical appliances, stainless steel products, steel structure construction, and interior decoration.
In summary, from manual operation to hydraulic and electric-driven machines, and now towards automation and intelligence, the shearing machine has become an indispensable part of the production process. With ongoing technological advancements, it is expected that shearing machines will continue to see innovation and improvements, providing more efficient and precise metal processing solutions for various industries.
About Us
Durmapress specializes in designing, manufacturing and selling various metal processing equipment, including bending machines, shears, punches, laser cutting machines, etc. The company was founded in 2000. With years of experience and technology accumulation. DurmaPress has become one of the well-known brands in China's metal processing machinery industry.
Contact Us
Recent Posts
Categories
Follow Us
Weekly New Video
Contact us for more information
If you have any information about our products, please contact us and we will reply within 24 hours.