Overview of common problems of plate shear
Common problems in the shearing process with a shearing machine can impact the quality and efficiency of processing. Uneven force during shearing can easily lead to bending and distortion of the plate, affecting its appearance and subsequent processing. To address this, optimizing process parameters and using a stable fixed device is essential to ensure better results.
The tool is not sharp or improper parameters produce burrs, affecting the appearance and subsequent processes, need to regularly check the tool, optimize process parameters, the use of de-burring technology.
Insufficient tool precision or uneven plate material leads to uneven surfaces, affecting the appearance, performance, and safety, need to improve tool precision, screening plate material, and advanced detection technology.
In summary, the problems in shearing need to be highly emphasized, and effective measures should be taken to solve them to ensure processing quality and efficiency.
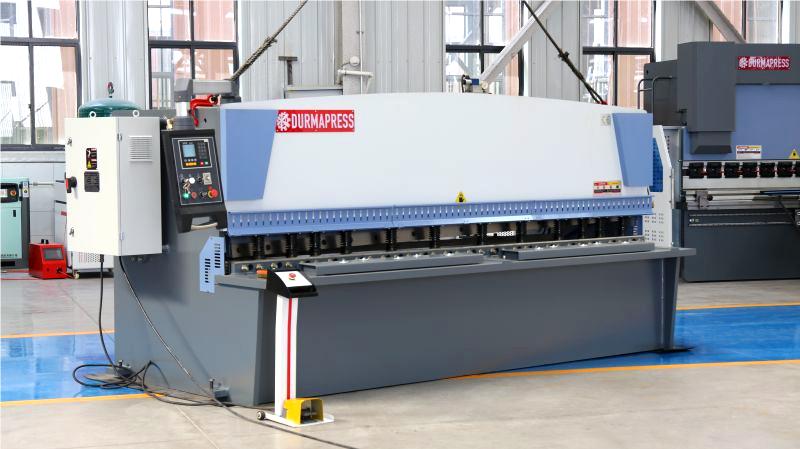
Causes and solutions of plate deformation
Problem Description
In the process of metal processing, after the plate is sheared, the phenomenon of warping or twisting often occurs. This deformation not only affects the flatness and aesthetics of the plate, but may also affect the subsequent processing and use. For example, warped plates may be difficult to assemble, resulting in reduced dimensional accuracy and even potential safety hazards.
Cause analysis
The causes of plate deformation mainly include the following aspects:
- Uneven force: When the plate is subjected to uneven force in the shearing process, it is easy to lead to plate warping or distortion, especially uneven thickness or different hardness of the plate is more likely to appear this problem.
- Improperly set shear pressure: If the shear pressure of the shearer is not set reasonably, it may make the shear process on the plate pressure is too large or too small, resulting in poor shear quality.
- Blade wear or inappropriate gap: long time use of the blade may appear wear, or blade gap is too large or uneven, affecting the effect of shear, thus causing deformation of the plate.
Solution
- Adjust the blade gap: Reasonably adjust the blade gap according to the thickness of the plate to ensure that the blade gap matches the plate, in order to reduce the extra pressure on the plate during the shearing process and prevent deformation.
- Ensure that the shear pressure is set correctly: according to the material and thickness of the plate, reasonable setting of the shear pressure to ensure that the shear force is uniform, thereby reducing deformation.
- Regular replacement of blades: Check the wear and tear of the blades in time, and grind or replace them regularly to ensure that the blades are always kept in the best condition.
Auxiliary measures
- Optimize the design and manufacture of equipment: By improving the overall design and structural stability of the shearing machine, reduce the excess stress on the plate when shearing.
- Strengthen operation training: professional training for operators to ensure that they can reasonably adjust the parameters of the equipment, the correct use of the shearing machine.
- Introduction of advanced detection technology: the use of high-precision testing equipment, real-time monitoring of the deformation of the plate in the shear process, and timely adjustment of operating parameters.
Causes and solutions of burrs
Problem description
The edges of the cut sheet metal are often rough or not smooth, which will reduce the quality of the product and increase the difficulty of subsequent processing. The presence of burrs may also lead to friction and abrasion during the subsequent use of the sheet, affecting the service life of the product.
Cause analysis
- Blades are not sharp or badly worn: blades are easy to become blunt after a while, especially when processing hard materials over a long period, blade wear increases, resulting in burrs on the edges of the metal when shearing.
- The plate is too thick, the shearer does not adapt: when the thickness of the plate exceeds the shear capacity of the shearer, the equipment can not accurately cut, resulting in rough edges of the shear.
- Blade gap is too large or uneven: improper adjustment of the blade gap will lead to uneven force during shearing, resulting in edge burrs.
Solution
- Regular replacement or grinding of blades: according to the frequency of use of the shearer and processing materials, regularly check the sharpness of the blades, timely grinding or replacement to ensure that the blades are always in good condition.
- Check whether the equipment is suitable for the current thickness of the plate: according to the processing needs, a reasonable choice of suitable thickness of the shearer, to avoid overloaded operation.
- Adjust the blade gap: the blade gap for accurate adjustment, so that it matches the thickness of the processed plate, reducing the drag caused by the shear process of burrs.
Shear uneven problems and solutions
Problem Description
After the plate is sheared, the shear line may not be straight, or the shear edge is uneven, which will directly affect the appearance quality of the product and the accuracy of subsequent processing.
Cause analysis
- The plate is not firmly fixed, moving during shearing: If the plate is not firmly fixed during shearing, the plate may move slightly during the shearing process, resulting in the shear line is not straight.
- Blade installation is not balanced, resulting in uneven distribution of shear force: If the blade installation angle is not correct, or the installation is not balanced, shear force will be uneven, affecting the quality of shear.
- Blade wear or improper installation angle: blade wear will lead to shear can not realize flat cutting, improper installation angle will also lead to poor shear effect.
Solution
- Ensure that the sheet is securely fixed before shearing: Use a clamping device or fixing tool to ensure that the sheet does not move during the shearing process and to maintain the straightness of the shear line.
- Adjust the installation position of the blade: ensure that the blade is installed smoothly and the shear force is evenly distributed to ensure the shear effect.
- Regularly check the blade wear: If the blade is worn, timely grinding or replacement, and adjust the installation angle to ensure it is parallel to the shear surface.
The importance of blade gap adjustment
The gap affects the shearing effect
The size of the blade gap directly affects the shearing effect. Too large a gap will lead to burrs and uneven cuts, while too small a gap may lead to jamming or cutting. Therefore, accurate adjustment of the blade gap is the key to ensure the quality of shear.
How to adjust the blade gap according to the thickness of the sheet
Different blade clearances need to be set for different thicknesses of sheet to ensure that the blade can cut the sheet smoothly without excess stress or damage.
Regular Inspection and Calibration
It is recommended to check and calibrate the blade gap regularly to ensure that the shear always maintains the best cutting accuracy and reduces processing errors.
Importance of proper lubrication
Effect of lubrication on shear accuracy
Proper lubrication can reduce the friction between the blades and the metal, reduce blade wear and improve shear accuracy. At the same time, lubrication can also extend the service life of the equipment and reduce maintenance costs.
Key parts of lubrication
Hydraulic system, blade bearings, guide rails, etc. are the parts that need to be lubricated regularly to keep them running smoothly and prevent the equipment from jamming or malfunctioning under high intensity use.
How to choose the right lubricant
Choose an efficient and durable lubricant to ensure that the equipment remains stable under prolonged operation and to reduce the loss of shear accuracy caused by wear and tear.
The need for blade replacement
The effect of blade wear on shear quality
When the blades are worn, the precision of the shear will be greatly reduced, prone to produce burrs and uneven shear, directly affecting the quality of the product.
How to determine the blade needs to be replaced
By observing the shear quality, listening to the operating noise, checking the surface of the blade whether there are obvious signs of wear and tear, etc., you can judge the use of the blade, timely replacement of the blade to maintain the shear effect.
Recommended cycle for blade replacement
According to the frequency of shearing, the hardness of the processed material and the use of the blade, it is recommended to replace the blade periodically to extend the service life of the equipment and ensure long-term efficient operation.
Conclusion
By regularly adjusting the blade gap, reasonably lubricating the key parts of the shearing machine, and replacing the blades in a timely manner, the common problems encountered in the shearing process can be effectively solved, and the working efficiency and shearing quality of the shearing machine can be significantly improved.
About Us
Durmapress specializes in designing, manufacturing and selling various metal processing equipment, including bending machines, shears, punches, laser cutting machines, etc. The company was founded in 2000. With years of experience and technology accumulation. DurmaPress has become one of the well-known brands in China's metal processing machinery industry.
Contact Us
Recent Posts
Categories
Follow Us
Weekly New Video
Contact us for more information
If you have any information about our products, please contact us and we will reply within 24 hours.