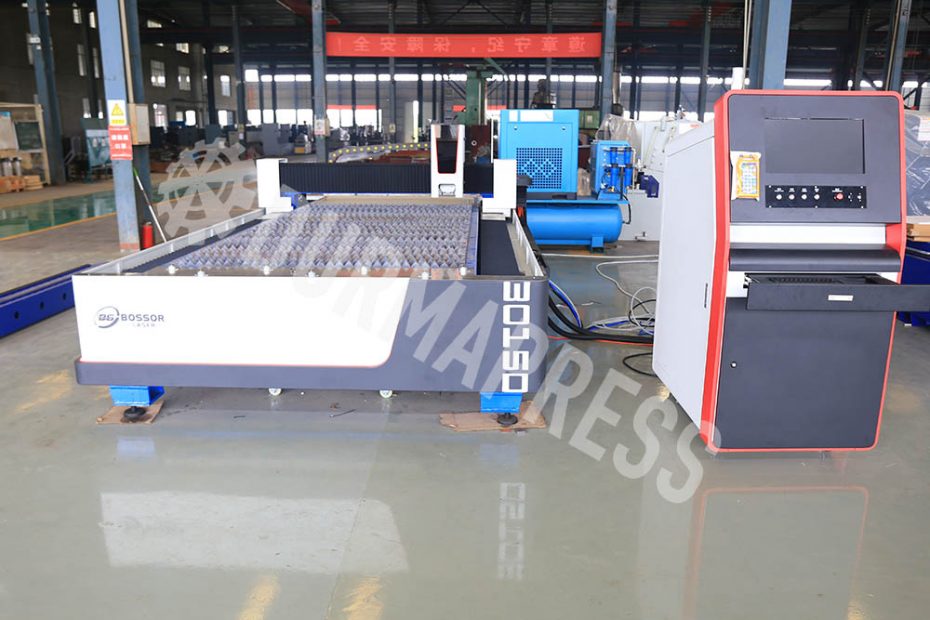
1. BS3015T-3000W Laser cutting machine and punching technology
Any thermal cutting technique, except in a few cases where it can be started from the edge of the board, generally must have a small hole through the board. Before the laser stamping compound machine is to punch out a hole, and then start cutting from the hole with the laser. There are two basic ways to punch a laser cutter without a stamping device:
Blasting perforation - The material is irradiated by a continuous laser to form a crater in the center, which is then quickly removed by a stream of oxygen coaxial with the laser beam to form a hole. Generally, the size of the hole is related to the thickness of the plate, and the average diameter of the blasting hole is half of the thickness of the plate. Therefore, the aperture of the blasting hole of the thicker plate is larger and not round, and it is not suitable for the parts with higher processing accuracy requirements, and can only be used for scrap. In addition, because the oxygen pressure used in the piercing is the same as when cutting, the splash is larger.
Pulse perforation -- the use of peak power pulse laser to melt or vaporize a small amount of material, commonly used air or nitrogen as auxiliary gas, in order to reduce the expansion of the hole due to exothermic oxidation, gas pressure is smaller than the oxygen pressure when cutting. Each laser pulse produces only a small jet of particles that go deeper and deeper, so it takes a few seconds to punch a thick plate. Once the perforation is complete, the auxiliary gas is replaced with oxygen immediately for cutting. This perforation diameter is smaller, its perforation quality is better than blasting perforation. The laser used for this purpose should not only have high output power; More important is the temporal and spatial characteristics of the beam, so the general cross-flow CO2 laser can not adapt to the requirements of laser cutting. In addition, pulse perforation also requires a more reliable gas control system to realize the gas type, gas pressure switching and perforation time control.
In the case of pulse perforation, the transition technique from pulse perforation when the workpiece is at rest to continuous cutting of the workpiece at the same speed should be emphasized in order to obtain a high quality cut. Theoretically speaking, it is usually possible to change the cutting conditions of the acceleration section, such as focal length, nozzle position, gas pressure, etc., but in fact, it is impossible to change the above conditions due to the short time. It is practical to change the average power of laser in industrial production. The specific method is to change the pulse width. Change the pulse frequency; Change the pulse width and frequency simultaneously. The actual results show that the third method has the best effect.
2. Analysis of the deformation of small holes (small diameter and thick plate) in cutting processing
This is because the machine tool (only for high-power laser cutting machine) uses pulse perforation (soft piercing) rather than blasting perforation when machining holes, which makes the laser energy too concentrated in a small area and scorches the non-processing area, causing the deformation of the hole and affecting the processing quality. At this time, we should change the pulse piercing (soft piercing) mode into blasting piercing (common piercing) mode in the processing program to solve the problem. But for the small power laser cutting machine is just the opposite, in the hole processing should take the way of pulse perforation to obtain better surface finish.
3 laser cutting low carbon steel, workpiece burr solution
According to the work and design principle of CO2 laser cutting, the following reasons are analyzed as the main causes of burring workpiece: the upper and lower positions of the laser focus are incorrect, the need to do the focus position test, adjust according to the focus offset; The output power of laser is not enough, need to check the laser generator work is normal, if normal, then observe the laser control button output value is correct, to be adjusted; Cutting line speed is too slow, need to increase the line speed in operation control; Cutting gas purity is not enough, need to provide high quality cutting gas; Laser focus offset, need to do focus position test, according to the focus of the offset to adjust; If the machine runs for a long time, the machine will need to be shut down and restarted.
4 laser cutting processing stainless steel and aluminum zinc plate, the workpiece has burr analysis
The emergence of the above situation, the first consideration of cutting low carbon steel burr factors, but not simply to speed up the cutting speed, because the increase in speed sometimes appear plate cutting does not wear, this situation is particularly prominent in processing aluminum zinc plate. At this time, other factors of the machine tool should be comprehensively considered to solve, such as whether the nozzle should be replaced, the unstable movement of the guide rail and so on.
5. Analysis of incomplete laser cutting through state
After analysis, it can be found that the following situations are the main causes of machining instability: the selection of laser head nozzle does not match the thickness of the machining plate; Laser cutting line speed is too fast, need to operate control to reduce the line speed; The nozzle induction is not allowed to lead to the laser focus position error is too large, the nozzle induction data need to be redetected, especially when cutting aluminum is most likely to occur.
6 cutting low carbon steel abnormal spark solution
This situation will affect the machining quality of the cutting surface finish of parts. At this time, under the condition that other parameters are normal, the following conditions should be considered: The loss of laser nozzle NOZZEL, should be replaced in time. In the case of no new nozzle replacement, the cutting gas pressure should be increased; The thread between the nozzle and the laser head is loose. Stop cutting immediately, check the connection status of the laser head, and reinstall the thread.